Executive summary
Tecesa Architectural Glass, located in Irapuato, Mexico, has grown from a small operation to a leading player in the glass manufacturing industry. By implementing FeneVision ERP software, Tecesa addressed challenges in data management and on-time delivery.
FeneVision’s flexibility, real-time tracking, and customer-centric approach enabled Tecesa to focus on delivering quality products while fostering customer trust. With dedicated Spanish-language support and robust features, Tecesa continues to thrive, setting new standards for the glass industry.
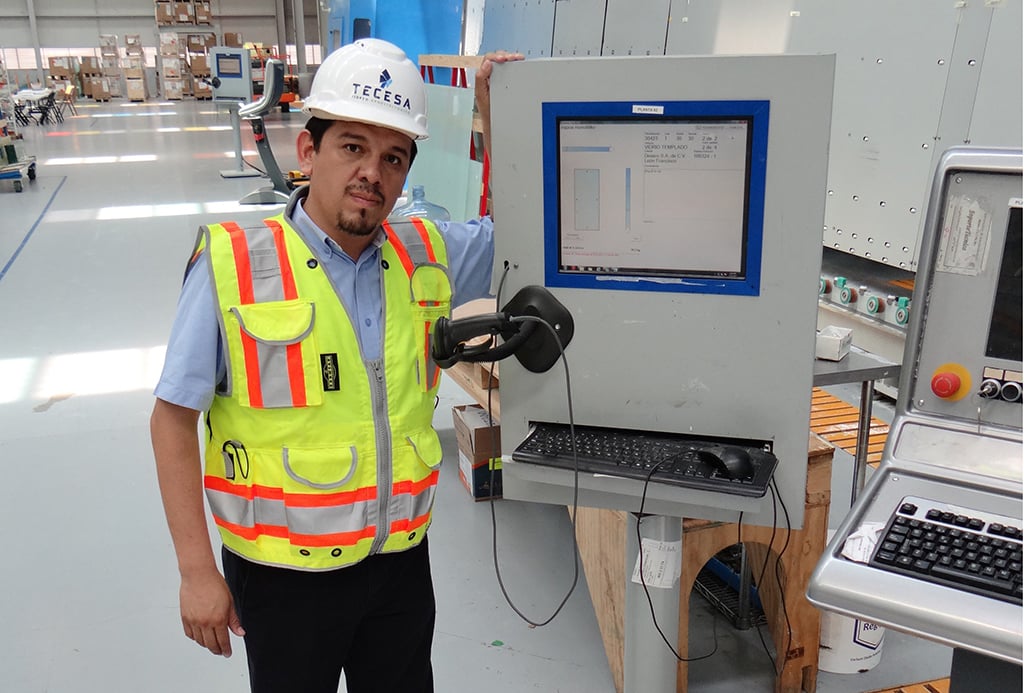
Why change was needed
Before implementing FeneVision, Tecesa struggled to maintain accurate, real-time production data, risking operational inefficiencies and missed customer expectations. Without a reliable ERP system, Tecesa faced challenges in:
- Tracking vital production information
- Managing data in real-time
- Ensuring on-time delivery and customer satisfaction
How change happened
Tecesa implemented FeneVision manufacturing ERP software, which provided the tools to centralize data, improve production workflows, and support real-time tracking. Key elements of the solution included:
- Full Spanish-language support for seamless communication
- Real-time production tracking and reporting
- Enhanced flexibility to adapt to TECESA’s unique requirements

What change delivered
Since adopting FeneVision, TECESA has seen remarkable improvements in operations and customer satisfaction:
- Streamlined production: Real-time data tracking minimizes errors and delays.
- Enhanced reliability: Improved on-time delivery strengthens customer trust.
- Operational focus: Tecesa can now concentrate on core business goals.
- Customer-first approach: Clients experience better service and higher-quality products.