Introduction
Bellmont, a leading cabinetry manufacturer, needed a way to accelerate product launches, improve production efficiency, and reduce manual processes. By implementing Insight, they streamlined their design-to-production workflow, allowing them to launch their District product line in half the time.
Insight enabled seamless integration between engineering, order processing, and shop floor execution, cutting lead times, reducing manual errors, and improving overall efficiency.
The Challenge
Time-consuming, manual processes
Bellmont relied on outdated systems that lacked the ability to handle complex configurations and customizations efficiently. Launching a new product line required extensive manual effort, slowing down production.
Disconnected workflows
Engineering, order entry, and manufacturing operated in silos, making it difficult to coordinate production schedules, track materials, and optimize machine processes.
Limited inventory visibility
Without real-time inventory tracking, managing material replenishment and minimizing waste was a challenge, leading to inefficiencies on the shop floor.
“Launching a complex product line like District required a solution that could handle multi-material, multi-finish configurations with precision and speed."
Dan Swanson, VP Product Marketing
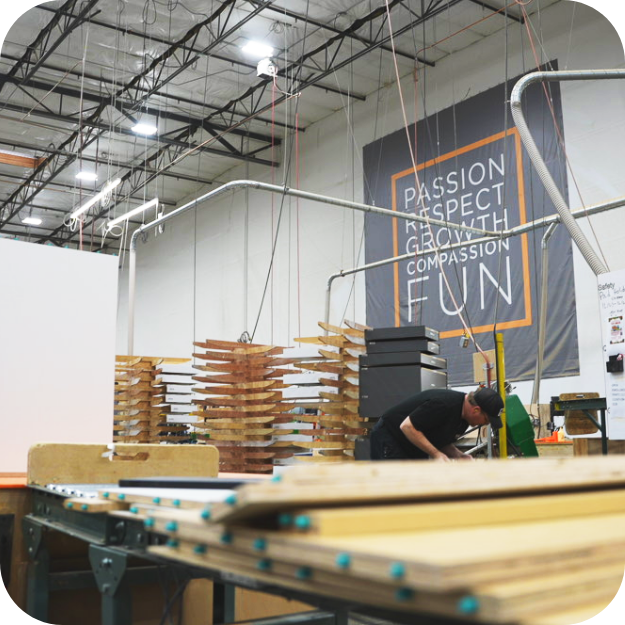
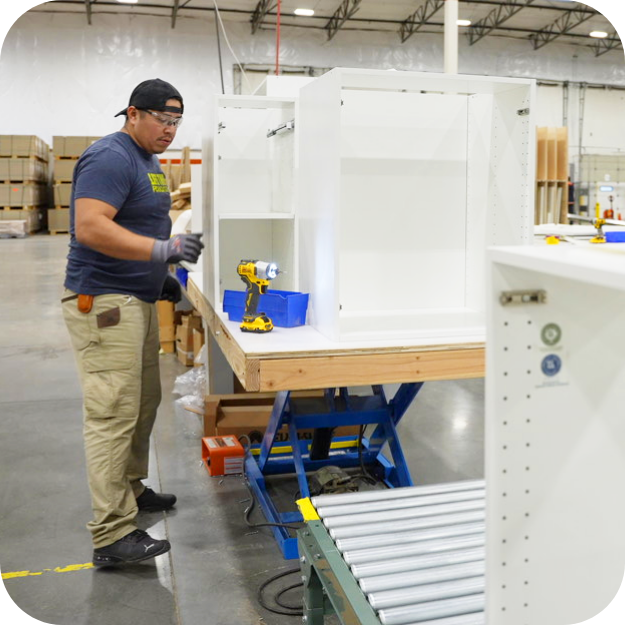
The Solution
The Results
Accelerated product launches
Bellmont successfully launched its District product line in just 6 months—half the time of previous launches.
Improved production efficiency
With automated scheduling, inventory tracking, and order management, Bellmont reduced lead times and improved throughput.
Fewer errors, better scalability
By eliminating manual data entry and streamlining processes, Insight enabled higher accuracy and smoother scaling for future product lines.